CERAMIC
Whether hand/slab built or wheel thrown, most pieces are first carved or stamped with original designs I have created, then each piece goes through an initial BISQUE firing to harden the piece to a permanent state but they still remains porous, allowing it to accept the glazes. Next I apply wax to areas I want resistant to glazes, then hand paint underglazes (chemically stable colored pigments) on to a variety of areas. Following this, I glaze-trail various areas, inlaying glazes into carved lines or other areas, frequently layering glazes for desired chemical interactions during the glaze firing process. My last step it to give each form a glaze dip, coating everything not waxed before the final GLAZE firing, typically to Cone 6 in an electric kiln.
When WHEEL-THROWING, I use the potter’s wheel as a tool in addition to creating hand formed additions like handles for functional wear or decorative elements. When HAND-BUILDING, my work is typically using slab construction. While I have utilizing a variety of clays, I now use Cone 6, mid-fire, B-Mix Clay, a porcelain-like white clay with a smooth consistency that is ideal for carving and stamping into. I have a basic pallet of six glazes (Blue, Brown, Yellow, Green, Clear and Waterfall Brown) that I mix myself. These combined with Amoco Velvet Underglazes give my work the brilliant color that people love in my work.
My CARVING work is very textural and references flora, fauna, natural rock formations, as well as animals, patterns and forms I relate to in underwater marine life. Despite using a limited amount of tools on each hand-carved piece, I strive to be fresh in every compositional arrangement and form. Like Henri Cartier-Bresson’s view of photography, each cut or texturizational decision I make is instinctively made at the “decisive moment”. I recognize that every variable I apply can entirely alter the pattern and from there the form. Further adding to the complexity, variations of clay additions, stretching the clay, creating textural impressions, applying slips and my various glaze processes continue to make each piece a truly unique, individual, one-of-a-kind object.
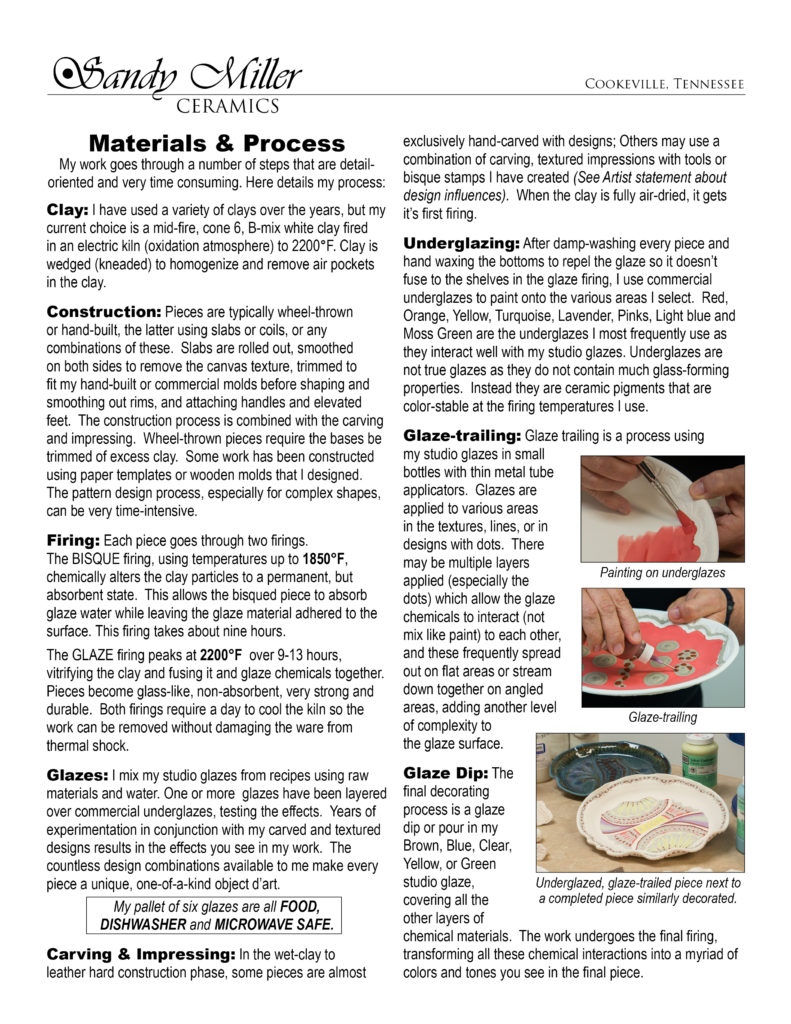
FLUID ART
For two years prior to 2021, I became fascinated by Fluid Acrylic Abstract Painting (aka Pour Painting) on the internet. The explosion of colors, mica sheen, and cells lead me to learn more about this technique. I now use commercial tiles, coasters and canvases to paint on with the method of four layers to create these works of art. The first layer called the “pillow” is a house paint; the second layer, called the “Pouring Medium”, is a mixture of varnish, untinted house paint, artist acrylic paints and in some, mica powders; the third layer is the “Cell Activator” which currently is a combination of Amsterdam White or Black acrylic paint added to Australian Floetrol. After painting and waiting three weeks for these three layers to cure, I add a layer of Stonecoat Resin, a two part epoxy which restores the brilliance of the mica and acrylic paints through the glass-like surface of resin. Stonecoat Resin is rated to 450˚F, making it idea for hot plate trivets. In addition to ceramics, I now produce a variety of functional and decorative work in Fluid Art.
POLYMER CLAY (Coming soon to my website)
In late 2022 I took a 3-hour polymer clay jewelry class and became excited about this material. In conjunction with the mica powders and resin in the fluid art, and my textured stamps and tools in ceramics, I began joining these materials and textures to the polymer clay to get textural effects and iridescent, colorful shimmering to their surfaces. The blending and stacking of the colored layers of clay can produce strident layers, marbling effect, caning*, and building of imagery within a single piece and I am continuing to explore this art form which ties into my love of color and texture – and my early love of polished rocks.
*A polymer clay cane is a log of polymer clay that’s made with a design that runs the entire length of the log. Slices from the cane will reveal a design and all slices from the cane will have identical designs. A polymer clay cane can be reduced by squeezing and compressing.